PCB CNC: Unterschied zwischen den Versionen
Zeile 125: | Zeile 125: | ||
Pins of through-hole mounted devices also do not form automatic top-bottom connections. This especially frustrating with the eagle autorouter, because I found no way of turning this off. Sometimes you can compensate by soldering also on the top side of the part, but very often there is really no space for that. Best thing is to manually overwork the board in eagle. | Pins of through-hole mounted devices also do not form automatic top-bottom connections. This especially frustrating with the eagle autorouter, because I found no way of turning this off. Sometimes you can compensate by soldering also on the top side of the part, but very often there is really no space for that. Best thing is to manually overwork the board in eagle. | ||
[[Datei:goodpad.png|center|thumb|400px|How to make your solder easier. | [[Datei:goodpad.png|center|thumb|400px|How to make your solder easier.]] | ||
=== Routing === | === Routing === | ||
Zeile 132: | Zeile 132: | ||
Then I move the wires around, so that the sidewards distance is maximized. This is done my making complete diagonals, and successively moving outer wires further outside. | Then I move the wires around, so that the sidewards distance is maximized. This is done my making complete diagonals, and successively moving outer wires further outside. | ||
[[Datei:brdgoodpad.png|thumb|center|800px| Example of good (not really, but sufficient) and bad wire placement". It is not a very good example, I will try to produce if there is time]] | [[Datei:brdgoodpad.png|thumb|center|800px| Example of good (not really good, but sufficient) and bad wire placement". It is not a very good example, I will try to produce if there is time]] | ||
=== Mounting Holes === | === Mounting Holes === | ||
Zeile 138: | Zeile 138: | ||
=== Isolation Distances === | === Isolation Distances === | ||
If you happen to work with larger voltages, you need isolated gaps on the PCB. I would do that by drawing a filled polygon on the bottom layer, or a group of overlapping or | If you happen to work with larger voltages, you need isolated gaps on the PCB. I would do that by drawing a filled polygon on the bottom layer, or a group of overlapping or connected wires, as if the isolation were a wire. | ||
After the milling, I would use a sharp | After the milling, I would use a sharp knife to lift the copper from the board at a corner, and peel it off. If you know the trick, it works quite well. | ||
[[Datei:peeledpcb.png|thumb|center|600px|A peeled off PCB. | [[Datei:peeledpcb.png|thumb|center|600px|A peeled off PCB. In this case, it is not an actual isolation distance, but just for the screws. You see here that I needed to peel off multiple areas. If I had connected the individual regions with overlapping wires, I could have saved some time.]] | ||
==Links== | ==Links== |
Version vom 28. Mai 2011, 07:34 Uhr
Introduction
CNCs can facilitate in the creation of PCBS:
- Manual etching and then using CNC to drill automatically.
- Cutting out the board , to have round PCBs, or similar.
- Automated isolation routing: From a PCB some surface parts are milled away, so that the connection copper area are left isolated.
Currently, all three steps are working on the Geilomat.
For the isolation, there is the normal approach, where all contours of copper areas are milled.
However much faster results can be obtained by milling the minimal path necessary to create the PCB-topology.
Some results are given in the soup of the Geilomat
- 0805 SMD resistors work fine, although the solder locations are not visible any more.
- It is possible to have one wire between the 2.54mm piched pins.
- Also 1.27mm pitch SMD chips are usually ok.
Examples
-
A normal isolated result.
-
A rather badly isloated and drilled PCB done on the Geilomat. Short circuiting copper flakes are visible on the center left.
-
A usually milled PCB, using pcb-gcode eagle plugin. This can be done by metaboard3.sh -tight
-
A voronoi milled PCB (left), a normally milled PCB, and a traditional PCB. Source
Time Consumption
For a complete, dense EuroPCB, expect about one hour of total time:
- 10 minutes for preperation, mounting and setup.
- 15 minutes for drilling/cutting.
- 20 minutes for the isolation of the bottom layer.
- 5 minutes for flipping/remounting/aligning
- 20 minutes for the top isolation
- 2 minutes for manual overworking the board.
For an arduino shield, expect about 30 minutes:
- 10 minutes for preperation, mounting and setup.
- 5 minutes for drilling/cutting.
- 5 minutes for the isolation of the bottom layer.
- 5 minutes for flipping/remounting/aligning
- 5 minutes for the top isolation
- 1 minutes for manual overworking the board.
Pros/Cons
Pros:
- Quite Faster than manual UV-exposing, etching and drilling.
- Cool
- No chemicals
- Good for high currents, as wired are wide.
- Cheaper PCB material. (Same area approx 50% the price)
- PCBs of up to 30x20 cm. However, flatness is problematic.
Cons:
- If the board is not mounted completely flat, the isolation might be not deep enough, and hence there are short circuits.
- Sometimes, flakes of copper short circuit neighboring copper areas. Usually at corners. A knife helps.
- Dust.
- Loud.
- Capacity between adjacent copper areas.
- Hotter soldering is required, as there are no thermal pads.
Metaboard*.sh
Metaboard are some bash shell scripts, that will automatically create cnc-paths in the form of gcode files. The starting point is the eagle .brd file. Download of the files: Here
Usage: metaboard3.sh <options> filename filename: eagle brd file to process
-double: create a double sided gcode -0.8: use a 0.8mm mill head instead of a 0.6 -tight: only offset by a distance of 0.3 mm -filled: the eagle board file has a filed dimension area instead of lines
It calls a couple of external programs:
- Eagle: to output the gerber files of the top and bottom layer
eagle: to call an ulp-program "drillbernhard.ulp" that outputs the drilling and cutting paths.- Eagle: to output the excellon drill files.
Visolate: To create the isolation paths. We use an unreleased version, that is scriptable.- Meanwhile, pcb2gcode was adopted and is used.
- grecode To mirror the board for second side. (Grecode was created especially for metaboard.sh by --Bkubicek 09:55, 26. Jul. 2010 (CEST))
While these are called, a couple of windows will pop up and hopefully disappear again. only shell output will be produced. you will get some debug images also in the current directory.
Usage
The workflow splits into the following points:
- Preperation: create an eagle brd file, copy it
- Metaboard*.sh: create the gcode files for the geilomat
- For the most current worflow use metaboard3.sh . It will require a 0.6 mm mill head, which is the best, as small IC holes are possible, and the tool length is so small that little sidewards forces are created. Hence, mill speed is larger than for 0.8mm tools.
- Setup:
- mount the board in the geilomat using double sided sticky tape.
- On the flat milled wood area.
- Which should be de-dusted first.
- Double sided tape should not overlap, as this creates 0.1mm height difference.
- Insert a suitable tool. Either a sharp Gravierstichel .
- EMC-setup: home the machine "home all", "touch off"/set coordinate system so milling will be on the actual board
Bottom layer:
- Isolation-milling: use the *back.ngc file created by metaboard3.sh
- drilling: use the *drill*.ngc file created by metaboard3.sh
- and cutting: use the *outline*.ngc file created by metaboard3.sh.
For single sided boards, the process stops here. Double sided boards are more sophisticated:
- Flipp the board, mounting it in any usefull position.
- Top layer:
- note down two drill hole coordinates from the drill file, in mm units.
- navigate using the joypad to the holes location on the flipped mounted PCB. Write down the coordinates of the special holes.
- call "grecode -align x1 y1 x2 y2 X1 Y1 X2 Y2 *front*.ngc > tmp.ngc" to rotate and shift. Maybe you have to change the signs of the x1 and x2, depending of the pcb2gcode version you use.
- Loading the tmp.ngc file just created
- check if the gcode is now aligned with the pcb.
- Isolate the top.
Removing the boards works best by using a twist motion around the z-axis. A brush should be nearby to clean the grooves.
Hints
VIAS


Milled vias form no automatic connection between top and bottom. You can solder them using a small copper wire. Or the magical Kupferhohlnieten.
If you change the diameter of your vias to 0.8, you can use the 0.6 inner diameter "Kupferhohlnieten". if you have a double side-connected pin of you 0.7 mm you might want to use a 1mm hole, to use the larger "hohlnieten", where you can then insert a 0.7mm pin.
Pins of through-hole mounted devices also do not form automatic top-bottom connections. This especially frustrating with the eagle autorouter, because I found no way of turning this off. Sometimes you can compensate by soldering also on the top side of the part, but very often there is really no space for that. Best thing is to manually overwork the board in eagle.
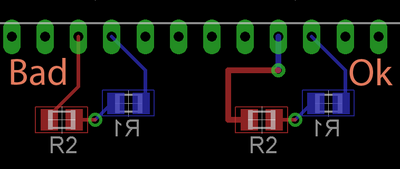
Routing
While the eagle autorouter tries to bundle wires closely together, for voronoi shaped pcbs, this is not so optimal. You can still use the autorouter, however I would recommend it only on the bottom layer. I use a 12.5 mil routing grid usually, and * for bottom N/A for top. Then I move the wires around, so that the sidewards distance is maximized. This is done my making complete diagonals, and successively moving outer wires further outside.
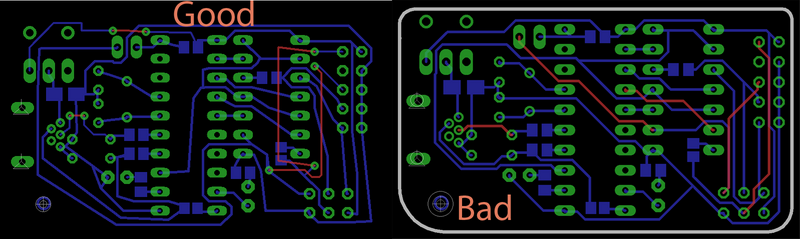
Mounting Holes
Currently PCB2Gcode does not respect mounting holes, meaning that it would grow the wires possibly in a way that two different signals could be short-circuited by the screw. To prevent this, place a bottom wire-arc around the screw. Then it gets it's own "pad".
Isolation Distances
If you happen to work with larger voltages, you need isolated gaps on the PCB. I would do that by drawing a filled polygon on the bottom layer, or a group of overlapping or connected wires, as if the isolation were a wire. After the milling, I would use a sharp knife to lift the copper from the board at a corner, and peel it off. If you know the trick, it works quite well.
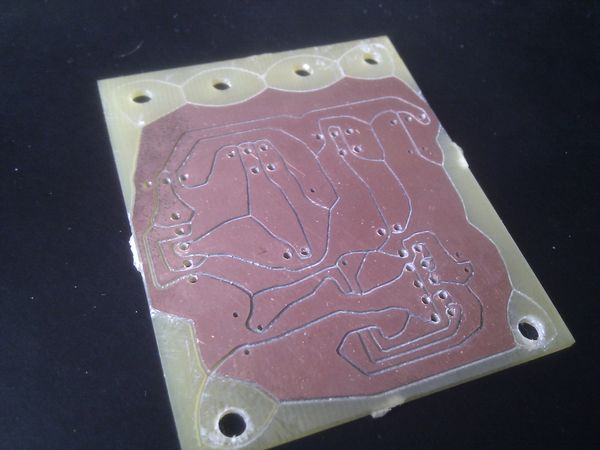